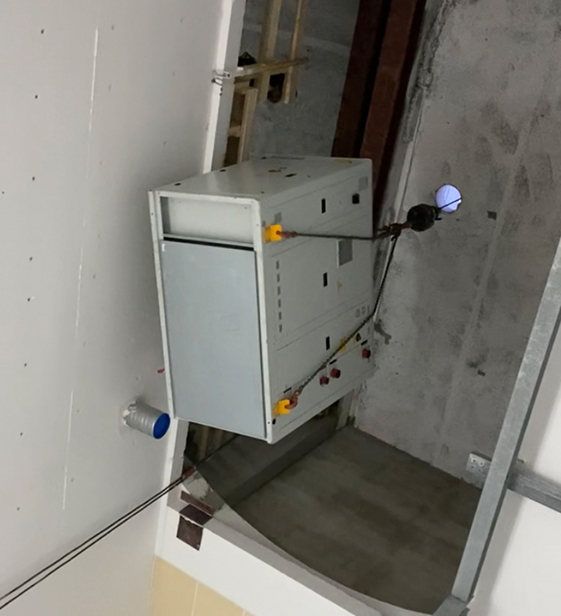
The Former US Embassy in Norway – HVAC Transported Underground Between Floors Using the Liftroller Floor
The Liftroller Floor system was used in a clever and effective way during the renovation of the former US Embassy in Oslo. The logistical challenge: three cooling units, each weighing 900 kg, needed to be transported several floors down inside the building. Thanks to the system’s flexibility and the solution-focused team at BVR AS, the challenge was resolved smoothly.
Project Overview
- Project: The Former US Embassy
- Type: Renovation
- Client: Bærums Verk Rørleggerbedrift AS
- Location: Oslo, Norway
- Liftroller System: Liftroller Wall
The former US Embassy in Oslo has been undergoing renovation since 2017, when the US authorities relocated. The building is soon to reopen as a public space featuring offices, hospitality, cultural venues, and a large rooftop terrace.
Smart Thinking + Innovative Equipment = A Job Well Done
One of the final installations involved placing three large cooling units several floors below ground level. The task was awarded to Bærums Verk Rørleggerbedrift AS (BVR AS). Lowering these 900 kg units through a floor opening to a level three floors underground required innovative thinking. How could they transport such heavy equipment safely and efficiently in an enclosed underground space with minimal headroom?
Thankfully, the team at BVR AS recognised the potential in the flexible Liftroller system. After consulting with Liftroller’s customer advisors, the Liftroller Floor model was selected as the ideal solution.
The Floor model is light enough to be carried down to basement level U1 and assembled above an opening in the floor, where a car lift is planned. A small hole was drilled in the ceiling above, just large enough to lower a crane hook from outside. Using a pallet jack, the cooling unit was positioned onto the Liftroller Floor, rolled across, and then lifted by the external crane. Once lifted, the Floor unit was pulled back and the cooling unit was lowered to the final level, where it was moved into place using the pallet jack.
Within minutes, the Floor model was ready to roll forward again and repeat the process for the remaining two units.
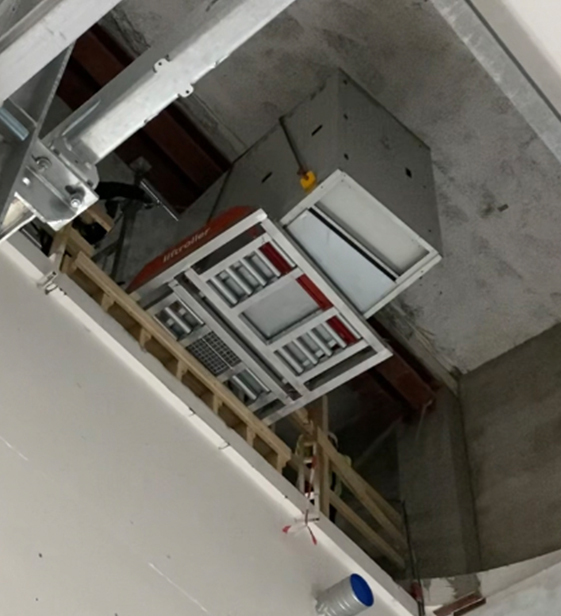